技术提供了管材制造的一体化
想象一个价值流,其中管道或管子被切割和弯曲。在工厂的另一个区域,加工环和其他机加工零件,然后送去组装进行钎焊或以其他方式安装到管端。现在想象同样的价值流,这次是终端成型。在这种情况下,端部成型不仅会扩大或减小管端直径,还会产生各种其他形式,从复杂的凹槽到复制先前钎焊到位的环的卷边。
在管材制造领域,端部成型技术悄然发展,制造技术在流程中引入了两个级别的自动化。首先,操作可以在一个工作范围内组合多个精密端部成型步骤——实际上,一个完成的设置。其次,这种复杂的端部成型已与其他管材和管道制造工艺相结合,如切割和弯曲。
自动化进步
大多数涉及此类自动化端部成型的应用都是在汽车和 HVAC 等行业中的高端精密管制造(通常是铜、铝或不锈钢)。在这里,端部成型消除了旨在确保空气或流体流动的无泄漏连接的机加工连接。这种管子的外径通常为 1.5 英寸或更小。
一些最先进的自动化单元开始于以线圈形式交付的小直径管。它首先通过矫直机,然后被切割成一定长度。之后,机器人或机械装置将工件运送到最终成型和弯曲。出现的顺序取决于应用要求,包括折弯和端部形状本身之间的距离。有时机器人可以携带单个工件从端部成型到弯曲再回到端部成型,如果应用需要两端都有端部成型的管子的话。
某些高端管端成型系统可以包含的制造步骤数量使此类电池的生产率更高。一些系统携带管子通过多达八个末端成型站。要开发这样的设置,首先要了解现代端部成型可以实现什么。
多工位端面成型
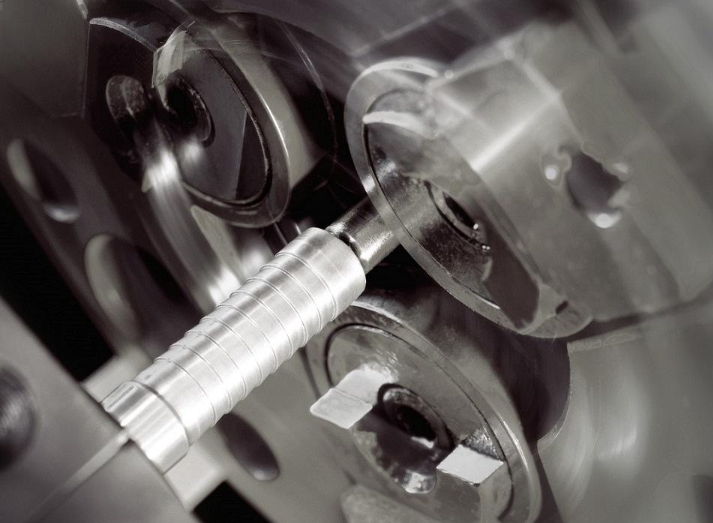
精密端部成型工具有多种。冲头冲头是管端成型的“硬工具”,可将管端缩小或扩大至所需直径。旋转工具可以倒角或对管进行端面加工,以确保无毛刺表面和一致的工艺。其他旋转工具执行滚动过程以创建凹槽、倒钩和其他几何形状(见图 1)。
端部成型顺序可能从倒角开始,这样可以提供干净的表面并确保夹具和管端之间的悬垂长度一致。接下来,冲压冲头执行卷边工艺(见图 2),膨胀和压缩管子,迫使多余的材料在外径 (OD) 周围形成一个环。根据几何形状,其他冲压冲头可能会在管外径上插入倒钩(这有助于将软管固定到管上)。旋转工具可能会在外径的一部分上开槽,然后是在表面上切削螺纹的工具。
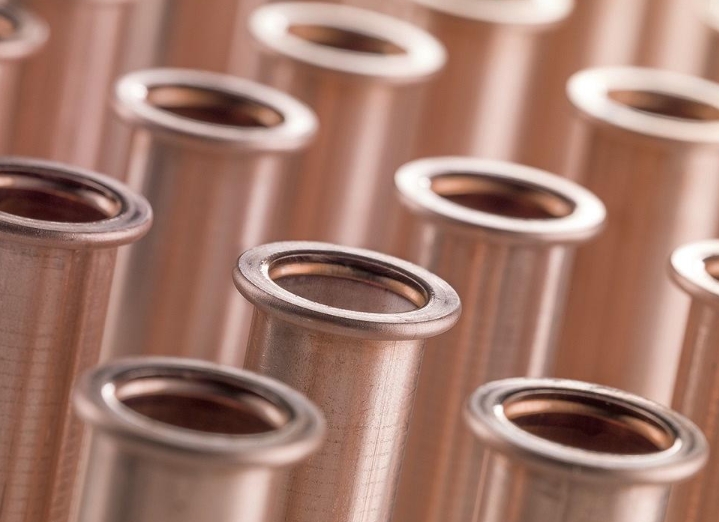
使用的工具和过程的确切顺序取决于应用程序。端部成型机的工作范围内有多达八个工位,序列可能非常广泛。例如,一系列冲头逐渐在管端形成一个珠子,一个冲头扩张管端,然后再用两个冲头压缩末端以形成珠子。在许多情况下,分三个步骤执行操作可以创建质量更好的珠子,而多工位末端成型系统使这种渐进操作成为可能。
末端成型程序对操作进行排序以获得最佳精度和可重复性。最新的全电动端部成型机可以精确控制其模具的位置。但除了倒角和攻丝之外,大多数末端成型加工步骤就是成型。金属形状如何因材料类型和质量而异。
再次考虑串珠过程(见图 3)。就像金属板中的闭合折边一样,端部成型中的闭合卷边没有间隙。这允许冲头将珠子形成到精确的位置。实际上,冲头是将珠子“冲压”成特定的形状。但是,类似于金属片中开口折边的开口珠子呢?在某些应用中,珠子中间的间隙可能会产生一些重复性问题——至少如果它的形成方式与封闭的珠子相同。冲压冲头可以形成开放的珠子,但由于没有任何东西从管内径 (ID) 支撑珠子,因此一个珠子的几何形状可能与下一个略有不同,这种公差差异可能是可接受的,也可能是不可接受的。
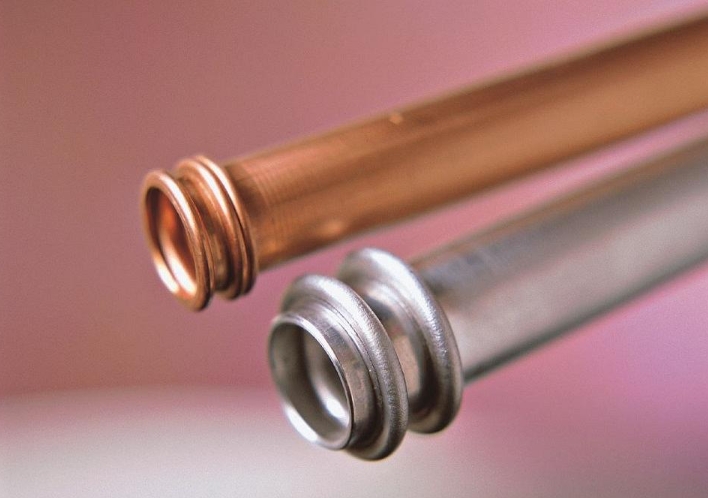
在大多数情况下,多工位端部成型机可以采用不同的方法。冲压冲头首先扩大管内径,在材料中形成波浪状预成型件。接下来,设计有所需胎圈负形状的三辊端部成型工具夹在管外径周围并滚动胎圈。
材料、工具和润滑剂
精密端部成型机可以创建各种形状,包括不对称形状。也就是说,末端成型确实有其局限性,其中大部分与材料的成型方式有关。材料只能承受一定比例的变形。
冲头表面热处理因设计形成的材料种类而异。他们的设计和表面处理考虑了不同程度的摩擦和其他随材料变化的最终成型变量。设计用于不锈钢管端部成型的冲头与设计用于铝管端部成型的冲头具有不同的特性。
不同的材料也需要不同种类的润滑。不锈钢等较硬的材料可能会使用较稠的矿物油,而铝或铜可能会使用无毒的油。润滑剂的应用方法也各不相同。旋转切割和滚压工艺通常使用油雾,而冲压成形可以使用溢流或油雾润滑剂。一些冲头有油直接从冲头进入管内径。
多工位端部成型机具有不同级别的冲头和夹紧力。在所有其他变量相同的情况下,与软铝相比,强度更高的不锈钢将需要更多的夹紧力和冲压力。
弯曲前还是弯曲后?
查看管端成型的特写镜头,您可以看到机器在夹具将管固定到位之前推进管。保持一致的悬垂——即金属超出夹具的长度——是至关重要的。对于可以移动到定义的停止点的直管,保持这种悬垂是很简单的。
当对先前弯曲的管进行末端成型时,情况发生了变化(见图 4)。弯曲过程可以稍微拉长管子,这增加了另一个尺寸变量。在这些设置中,轨道切割和端面工具可以切割和精加工管端,以确保它按照程序准确地位于应有的位置。
这就引出了一个问题,为什么弯曲后最终形成管子?它与工具和工件夹具有关。在许多情况下,端部模板放置得非常靠近折弯本身,在折弯循环期间没有留下直线部分供折弯机工具夹紧。在这些情况下,弯曲管子并将其转移到端部成型要容易得多,在那里它被固定在与弯曲半径相匹配的夹具中。从那里,端部成型机切断多余的材料,然后创建所需的端部成型几何形状(同样,最终非常接近弯曲)。
在其他情况下,弯曲前的端部成型可能会导致旋转拉伸过程复杂化,尤其是当端部形状干扰弯曲工具时。例如,夹紧管子进行弯曲可能会导致先前制成的端部形状变形。创建不会损坏最终形状几何形状的弯曲设置最终会带来更多麻烦,而不是它的价值。在这些情况下,在弯曲后结束形成管子更容易且更具成本效益。
设计自动化单元
采用端部成型的电池可能涉及许多其他管材制造工艺(见图 5)。一些系统同时具有弯曲和端部成型,考虑到这两个过程的联系程度,这是一种常见的组合。一些应用从端部成型直管开始,然后转向旋转拉伸弯曲以形成半径,然后返回端部成型机在管的另一端工作。
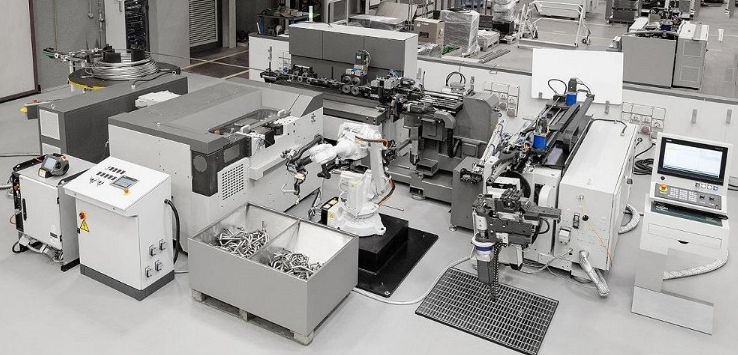
在这种情况下,顺序控制过程变量。例如,由于第二次端部成型操作发生在弯曲之后,端部成型机中的轨道切断和端面操作确保了一致的悬垂长度和质量更好的端部形状。材料越一致,最终成型过程的重复性就越好。
无论自动化单元采用何种工艺组合——无论是弯曲和端部成型,还是从管材成卷开始的单元——管材在各个阶段的进展方式取决于应用要求。在一些系统中,管材直接从卷材通过调平系统送入旋转拉伸弯管机的夹具中。当端部成型系统移动到位时,这些夹具会固定住管子。一旦端部成型系统完成其循环,旋转拉伸弯曲机就会开始。弯曲后,工具切割完成的工件。该系统可以设计为运行不同的直径,在端部成形器中使用专用冲压冲头,在左手和右手旋转拉弯机中使用堆叠工具。
但是,如果弯曲应用需要管 ID 中的球心轴,则设置将不起作用,因为送入弯曲过程的管直接来自线圈。这种安排也不适用于两端都需要形状的管子。
在这些情况下,涉及机械传输和机器人技术的某种组合的单元可能就足够了。例如,可以对管子进行开卷、整平、切割,然后让机器人将切割件放入旋转拉伸弯曲机中,在弯曲机中可以插入球心轴以防止弯曲过程中管壁变形。从那里,机器人可以将弯曲的管子转移到端部成型器上。当然,操作顺序可能会有所不同,具体取决于工作要求。
此类系统可用于大批量生产或小批量加工,例如,一种形状的 5 个、另一种形状的 10 个以及另一种形状的 200 个零件。机器设计也可能因操作顺序而异,尤其是在定位夹具和为各种工件提供所需间隙时(见图 6)。例如,接受弯管的端部成型中的定位夹必须有足够的间隙,以使弯管始终如一地定位。
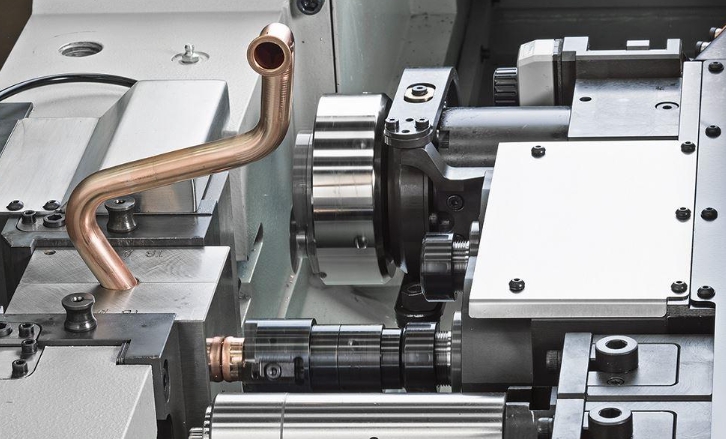
正确的顺序可以允许并发操作。例如,机器人可以将管子放入端部成型机中;然后,随着端成型机的循环,机器人可以将另一根管子输送到旋转拉伸弯管机。
新视野
对于新安装的系统,程序员将为工作组合设置模板。对于端部成型,这可能涉及冲压冲程进给速度、冲压机和夹具之间的中心或滚压操作的转数等细节。但是,一旦设置了这些模板,编程就变得快速而直接,程序员可以调整顺序并最初设置参数以适应手头的应用程序。
此类系统还设置为在工业 4.0 环境中连接,预测维护工具测量电机温度和其他细节,以及机器监控(如在特定时期生产多少零件)。
在地平线上,端部成型只会变得更加灵活。同样,该过程在变形百分比方面有局限性。尽管如此,没有什么能阻止创意工程师设计独特的端部成型装置。在某些操作中,冲压冲头插入管内径,并使管在夹具本身内的空腔中膨胀。某些工具可以创建延伸 45 度的端部形状,从而形成不对称的形状。
所有这一切的基础都来自多工位端部成型机的功能。当操作可以“一次完成”时,就会出现各种最终成型机会。